APPLICATIONS OF INSULATED METAL PANELS – Globe Panels
CIVIL ROOFS
1) TWO REGULAR PITCHES
For this type of standard roof, the roof panels are supplied in the length of the pitch. We establish the length considering the front position compared to the eaves gutter model (drawing 1). The panel is generally installed on a frame consisting of horizontally positioned wood strips. The position of the first strip where the eaves gutter fin will be hooked to and of the last strip positioned at least 20 cm from the ridge cap line, is very important, to allow the simultaneous fixing of shaped ridge cap-panel-strip (drawing 2). General rules advise fitting fixing groups on all the panel ribs on the two supports. We recommend the use of the silhouette profiles to protect the panel heads from atmospheric agents and guarantee the roof durability.
2) FOUR REGULAR PITCHES
This type of roof fastening is the same as for two-pitches roofs but requires panels with a slanted cut (use a suitable cutting tool). All panels are supplied in the measure corresponding to the maximum height of the pitch (drawing 3). Each panel will be cut diagonally following the ridge cap line, and the excess piece will be used for the opposite side of the next pitch (drawing 4). using this method, the production waste is reduced to the minimum. We recommend carrying out the diagonal cuts on the ground rather than on the roof. Therefore, you avoid damaging the panels that have already been installed. The ridge cap lines will then be covered with a specific metal ridge cap, not shaped or to be shaped during installation since the shaping varies depending on the slope of the pitches.
3) IRREGULAR PITCHES
Follow the indications described for the two cases above. The difference consists of the dimension and method of
installing the panels. In the case of irregular triangular pitches, a range of progressive sizes will be established for the panels to be cut diagonally (drawing 5). With this method, the excess piece will unlikely be used for other pitches and will, therefore, be discarded. Also, in this case, the metal joint ridge cap must be accurately prepared. It is generally advisable to order at least one or two additional sheets of the maximum length to be sure to complete the roof also in case of a cutting error during installation.
4) SUB TILE
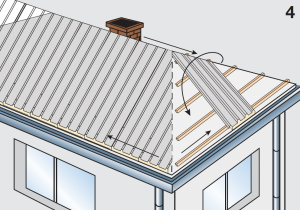
Thanks to its thermal insulation properties, we can also use the roof panel in brick roof systems, particularly as a sub-tile element. As regards the model, we recommend the use of a panel with the external ribbed metal facing and the internal facing made of roofing felt, to be applied directly to the slab.
There are two recommended installation methods. Either install the roof panel on which a frame of wood strips must be fitted in an orthogonal direction to fix the standard tiles (Drawing 6). Or exploit the pitch of the panel ribs to fit the traditional tiles directly to this, following the concave-convex system (drawing 7). In this case, it is necessary to add a metal tile stop profile on the starting side, or in any case, guarantee suitable fastening. In this case, we highly recommend using the silhouette profile.
INDUSTRIAL ROOF
1) TWO PITCHES-STEEL STRUCTURE
For this type of architectural structure, it is advisable to use roof panels with external and internal steel facings. To prevent any complications due to metal thermal expansion, we recommend selecting aluminum for the external-facing only if the length of the pitches does not exceed 10 meters. For all pitches longer than 13 meters, it is advisable to provide an overlapping element on central support (Drawing 8).
Here are the main indications for this type of work: apply a suitable linear seal lining on the panel joints to prevent any condensation (Drawing 9). When installing the ridge cap, use the ribbed sponge seal lining, available on request, and bend the flat end part of the panel with a pair of pliers where it meets the ridge cap, to prevent infiltration caused by a strong wind. Apply a metal sub ridge cap to close the ridge cap line between the two pitches and inject polyurethane foam between the panels (Drawing 10).
2) SHED ROOF
Shed roof does not require particular techniques since, in general, the very steep pitch guarantees a good water flow. To find an excellent joining solution between the sloping pitch made of panels and the vertical glazed structure, we recommend creating a special closure flashing according to the customer’s design and shaped to be combined with the ribbed panel (Drawing 11).
3) ROOF FOR PREFABRICATED STRUCTURE
In concrete prefabricated building construction, the insulating panel can be used as an alternative to curved connection panels between “y” beams, with considerable saving (Drawing 12) or to cover the whole roof, often in combination with fixed polycarbonate or glass-reinforced plastic roo flights. In the latter case, it may be necessary to bend the panel slightly to adapt it to the structure of the prefabricated building tiled roof. It is, therefore, possible to exploit the elastic characteristics of the panel components and adjust it to the slight bend of the tiled roof, remembering that the polyurethane foam should not have a thickness of over 40 mm. If the panel has to be fixed directly to the tiled roof, its lower support must be made of centesimal aluminum or roofing felt (Drawing 13), while if it has to be fixed to a metal structure or combined with fixed roof lights, its lower support must be made of steel.
In these two cases, the number of fixing groups must be increased, and the rules for the length of the panels must be
complied with as well. If overlapping operations have to be carried out, as frequently occurs in these cases, it is an excellent rule to subdivide the total length into three to avoid overlapping at the highest point (Drawing 14). On the other hand, we do not advise to use the panel with a narrower bending radius, since the external and internal metal facing could be scratched. The polyurethane foam would lose continuity.
EXTERNAL CLADDING
1) ASSEMBLY INSTRUCTIONS
The assembly of wall panels foresees the application of self-tapping screws applied from the exterior towards the interior. In general, the screw must join the two fins of the female screw and the male screw of two contiguous panels. Moreover, in the proximity of end (external and internal) supports, it is suggested to apply a safety screw at the center (Drawing 15). Please pay particular attention to the power of the electric screwer because an excessive force towards the interior could scratch the external panel surface. Regardless of the panel thickness, the support structure must foresee horizontal currents located at a maximum distance of 3.5 m in case of possible cuts to perform during the installation. To avoid following degradation phenomena we recommend to clean properly from off-cuts the borders. These operations are often foreseen when a connection at an orthogonal angle must be made between the walls.
2) FINISHING
The use of the wall panel foresees a series of finishes that render the covering work functional and aesthetic. There are two types of prepainted steel or aluminum profiles – not necessarily of the same color as the panel. The first one includes structural support profiles, such as horizontal elements on the ground and top (with “u,” “l,” or “z” shape according to the design) or internal vertical elements (in general with “u” or “l” shape). These profiles are generally of high thickness, of 8/10 or 10/10, according to the selected material. They foresee an anchoring to the panel or the building structure through self-tapping screws (Drawing 16).
The second type includes profiles with no structural function. The help to cover the joints between the angular walls or special joints, and they are generally 5/10 thick. To anchor to the panel only with steel rivets (Drawing 17).